Warehouse Control System Online Reports
Take warehouse productivity to a whole new level
When you manage a single warehouse, you can look around the space and generally see what’s going on. But when you manage a fulfillment network with multiple warehouses and fulfillment centers, you need hard data and easy-to-use reports to keep track of inventory levels and everything going on in each location.
Logiwa’s online reports are an invaluable part of our warehouse control system. Our reports make it easy to track and monitor every action in your warehouse, knowing the who, where, how and when for every movement.
Logiwa has pre-built reports that track inventory levels, orders, shipments, returns, and employee activities across all of your locations. Available-to-promise reports help you make the right buying decisions, and multi-warehouse inventory reports help you prevent shortages and manage inventory transfers with ease. And most importantly, our reports are easy to update so you see exactly what you want to see in each report, and you can run them from anywhere on any device.
Our warehouse control system and online reports let you track, manage and report on everything that happens in each location:
- Inventory & receiving
- Shipment & billing
- Available to promise
- User performance & workload
- Transaction history / movements
- Receiving report
- Compare receiving with PO
- Receiving serial report
- Inventory report
- Consolidated Inventory report
- Listing Inventory report
- Available to Promise
- External Inventory (Amazon FBA)
- Inventory to Produce
- Kit Inventory
- Tracking Report
- Lot and expiry date report
- Inventory Serial Report
- Shipment transaction report
- Warehouse progress report
- Order sales report
- Store based sales report
- Consolidated shipments report
- Shipped serial numbers report
Everything brands, online sellers and 3PLs need to achieve high-volume fulfillment success
Check out all the functionality we provide and then just imagine all of this power running in your fully digital warehouses and across your integrated fulfillment network. Serious results.
- Receiving
- Directed putaway
- Picking and packing
- PICK-FACE replenishment
- Return management
- Cycle counting
- Inventory transfers
- Multi-warehouse operations
- Multi-client operations
- Shipment rule automation
- DTC packing station
- Kitting and bundling
- Scale integrations
- Order routing
- Putaway automation rules
- Inventory allocation automation rules
- Automate picking job creation
- Shipment box suggestions
- Walking path optimization
- Put-to-wall
- Robotics integration
Logiwa makes a fast impact on your business
40%
increase in labor efficiency
3x
more orders shipped after first three months on Logiwa
8%
lower shipping costs with Logiwa rate shopping



Go beyond legacy WMS with Logiwa IO
When it comes to meeting modern demand, traditional warehouse management systems can’t keep up. Logiwa’s all-in-one FMS offers an agile, scalable solution to meet your changing business needs.
AI-driven Optimization
Streamline operations with waves and jobs for enhanced outbound flow. Monitor on-ground activities to optimize workforce management with labor standards.
Headless Architecture
Groundbreaking headless, versionless, and serverless architecture. Seamlessly adapt your operations to changing needs, design your own add-ons, and scale effortlessly.
Intuitive UI/UX
Ensures an engaging user experience with an intuitive app design. Onboard new employees in hours, not days.
Logiwa Marketplace
Our partner ecosystem allows you to add features and modules—your own, and those from the marketplace—for limitless configurability and continuous innovation.
Customer Success
See what our customers say
FAQs about Warehouse Control System
What is warehouse control system (WCS)?
How warehouse control system works?
What is the difference between WMS and WCS?
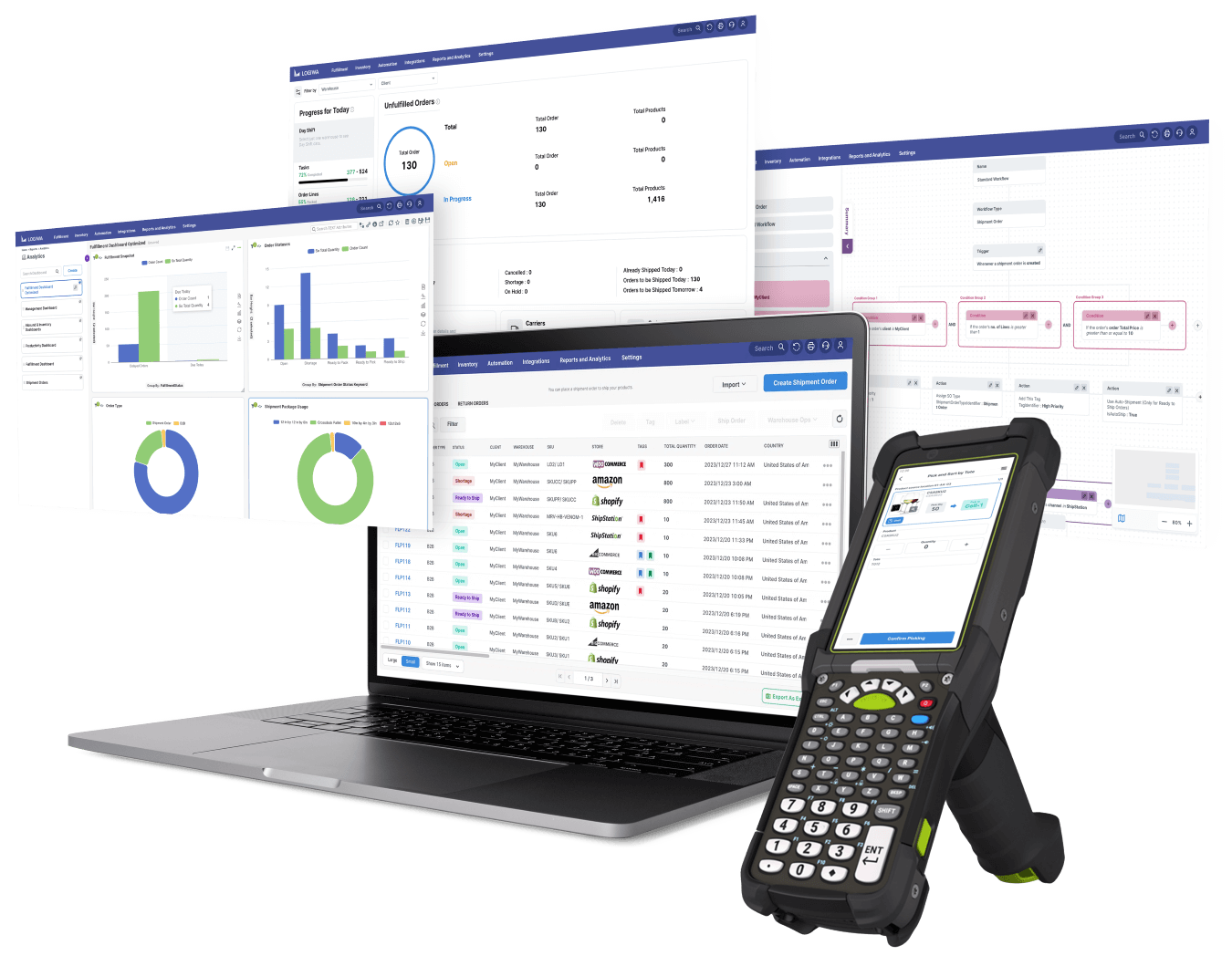