Fulfillment management is constantly evolving thanks to the rapid influx and development of transformative technology like artificial intelligence (AI) job optimization, enhanced personalization, automation and robotics, and green logistics. While all these advances are on track to foster substantial changes, AI job optimization boasts the most game-changing power in DTC fulfillment.
AI job optimization employs AI technology to analyze operational data such as stock levels,shipping details, pick routes, and order details. It then leverages derived insights to optimize picking and packing operations by automating job creation in the warehouse.
In today’s dynamic DTC ecommerce environment, brands using AI have a competitive edge when it comes to overall fulfillment efficiency. Thankfully, ecommerce businesses can utilize Logiwa IO’s AI job optimization add-on to automate job creation for pickers and packers, and enjoy substantial time-savings and productivity gains.
Contents
- The growing need for AI in DTC ecommerce fulfillment
- Understanding AI job optimization
- Logiwa IO and its AI job optimization feature
- Benefits of AI job optimization in fulfillment management networks
- AI is here to take over fulfillment management. Take advantage early.
- FAQs about AI job optimization for fulfillment
The growing need for AI in DTC ecommerce fulfillment
DTC fulfillment standards have continually been on the rise, as customers expect better fulfillment speed and experience with each order. So much so that 24% of today’s customers expect delivery within 2 hours. To achieve such super-fast delivery times, online retailers must first deal with the background factors that can curtail fulfillment management. They include:
- Volume handling: Inventory volume can grow rapidly and exceed warehouse space and handling personnel. It can also fluctuate quickly, wasting warehouse space.
- Order accuracy: Relying on manual or rule-based order processing leads to high error rates, especially when orders snowball beyond processing capacity.
- Operations management: Manually assigning job tasks to an overwhelmed workforce creates efficiency gaps that slow down or paralyze the fulfillment process.
How AI job optimization addresses fulfillment challenges
AI job optimization addresses many variables to help fulfillment centers achieve significant time savings. AI jobs can be scheduled or run manually at any time. Automating task allocation processes ensures fulfillment operations run efficiently 24/7.
Understanding AI job optimization
AI job optimization configures jobs and tasks and groups them to optimize for efficiency. To maximize efficiency during job regrouping, the AI engine considers the following aspects of order processing:
- Product specifications: Artificial intelligence considers order details such as size, fragility, and weight and assigns the most efficient picking and packing workflows, enhancing overall operational productivity.
- Picking location: In addition to considering specified picking priorities AI analyzes all workflows and groups tasks accordingly. With intelligent groupings, there are fewer repeated visits to the same locations. As a result, AI jobs visit 40% fewer picking and packing locations.
- Cart/tote optimization: AI analyzes cart/tote volumes and dimensions to create tote-based workflows. Each tote can contain entirely different jobs or multiple orders—ensuring each tote is filled optimally.
Key components of AI job optimization systems
AI job systems can rapidly process huge amounts of data to revolutionize picking and packing:
- Machine learning algorithms: Analyze and learn from operational data and facilitate continuous process improvement and create picking batches that maximize the use of mobile carts to greatly improve your efficiencies.
- Analytics: AI considers multiple possible solutions, thousands of possibilities in just seconds, and returns the most optimal job groupings.
Artificial intelligence’s analytics ability helps online retailers make sense of their operational data and glean crucial insights in every operational facet. Fulfillment centers bank on these data-based insights to make daily decisions that keep them both ahead of the competition and well-prepared for future trends.
Logiwa IO and its AI job optimization feature
Logiwa IO’s AI job optimization feature comes as an add-on requiring users to subscribe and liaise with a customer success manager (CSM) to complete installation.
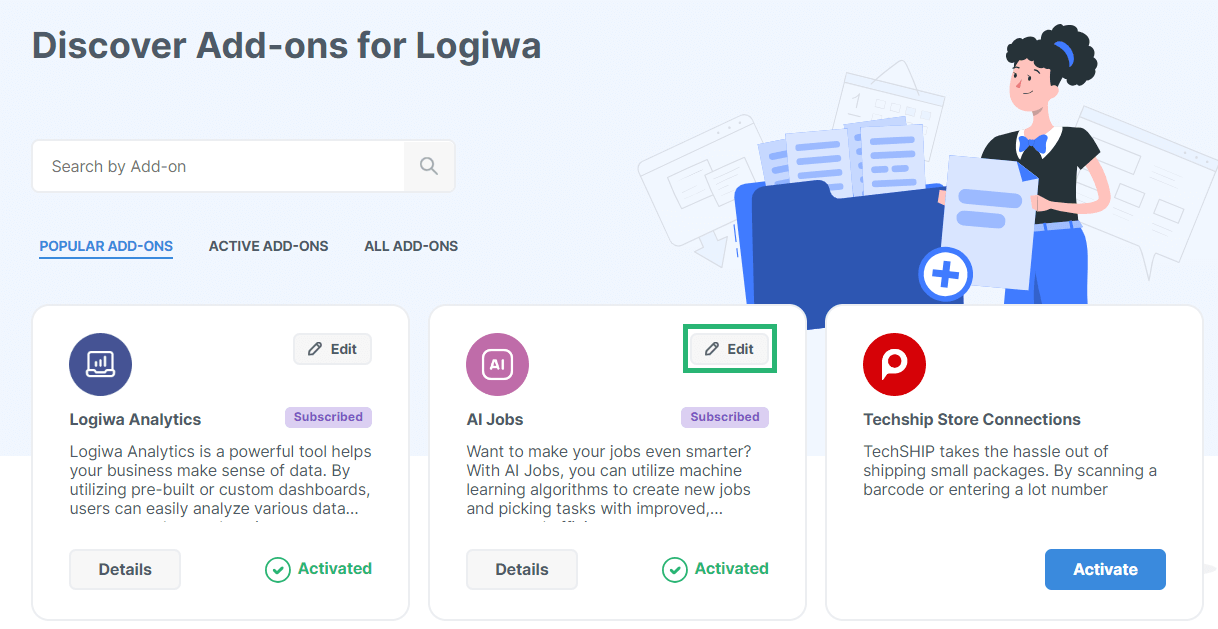
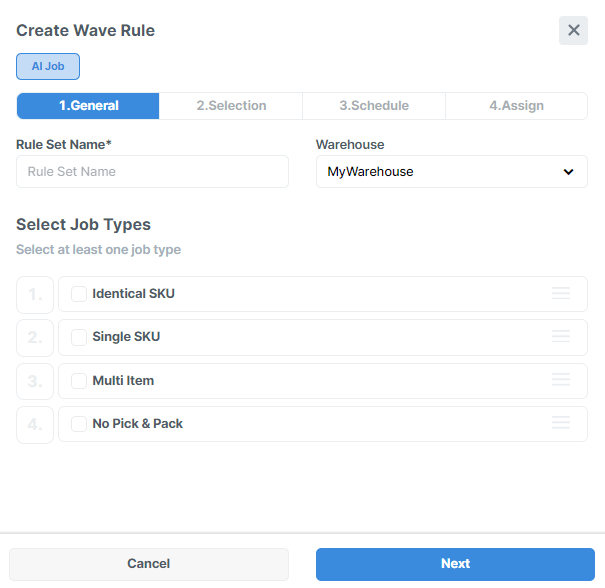
When the Wave Rule runs, Logiwa IOs AI considers multiple solutions from thousands of possibilities in just seconds, and returns the most optimal job and task groupings. These include:
- Batch pick flows: Items are picked in batches, and the Logiwa system bulk prints labels
- Tote-based flows: The Logiwa system prints labels according to the job type in each tote
Some popular job types supported by this feature include:
- Multi item Cluster Pick: Picking and sorting are done together
- Single Item Batch Pick: Orders are picked in bulk
- Identical Order and Identical Item Batch Pick: Similar orders picked together, with labels batch printed
- Single Item Cluster Pick: Multiple SKUs each picked to separate totes
Logiwa IO’s AI algorithms analyze large volumes of operational data and groups your orders into the most optimal workflows for efficient high-volume processing. It’s designed to streamline job processes, especially picking and packing operations. Logiwa IO’s user-friendly UX/UI also makes navigation easy for everyone, from floor warehouse workers to store executives.
Bonus: Watch our recent webcast “AI-driven order fulfillment” to hear a real-world use case of how Logiwa IO drives incredible improvements in the order fulfillment process.
Benefits of AI job optimization in fulfillment management networks
Fulfillment centers and management networks that use AI enjoy many benefits.
Improvements in productivity and operational speed
AI job optimization boosts overall efficiency up to 58% compared to manual completion. Such productivity gains help DTC brands scale fast without diluting their service or product quality.
Fewer human errors and more accurate order fulfillment processes
Automating repetitive fulfillment tasks like picking and packing substantially reduces error rates. We’ve seen our AI-driven jobs enable a team of pickers to pick the same quantity of items in 44% less time, as well as enable the same amount of orders to be packed in 10% less time at the packing station because of the optimized order grouping.
Substantial cost savings thanks to resource allocation optimization
AI empowers DTC ecommerce brands to allocate resources more feasibly. Compared to paper-based job assignments, one Logiwa IO customer went from 76 hours down to 32 hours to complete all their tasks on a typical day. This efficient resource use and allocation via AI yields enormous short- and long-term cost savings.
Enhanced customer satisfaction and competitive advantage
AI is instrumental in achieving and maintaining excellent customer experience and satisfaction. All components of AI job optimization collaborate to help brands fulfill brilliantly and continually elevate customer satisfaction.
AI is here to take over fulfillment management. Take advantage early
AI is transforming DTC ecommerce fulfillment for the better. AI has tentacles in all fulfillment areas, from enhancing and maintaining operational efficiency to guaranteeing order accuracy. DTC brands should pivot early and get a head start optimizing DTC fulfillment.
To experience Logiwa IO’s AI job optimization, contact one of our CSMs today to schedule a demo.
FAQs about AI job optimization for fulfillment
How does AI improve warehouse efficiency?
AI algorithms drive incredible efficiencies in picking, packing, and inventory management tasks, making operations more efficient.
Can AI help in inventory management?
Yes. AI supports intelligent inventory management by tracking stock levels to prevent stockouts or overstocks.
What role does AI play in optimizing order picking?
Logiwa IO uses advanced algorithms and machine learning to create picking batches that maximize the use of mobile carts to greatly improve efficiencies. AI considers multiple possible solutions, thousands of possibilities in just seconds, and returns the most optimal job groupings.
Transform your operations with Logiwa IO’s advanced technology.
Warehouse Management
Modern digital WMS powers a modern fulfillment experience